Pssst. Want a competitive advantage? Yes. Well read on, but keep it to yourself.
The telco industry is starting to get very, very busy. It’s ramping up for 5G deployments and people are already working extremely hard, with much more work to come. So, setting up efficient processes now has never been more important.
What follows is an example of how one of our customers is using Audicas to complete EME surveys in real-time. They estimate that it’s halved the total time to get a survey completed and that it has allowed their design teams back in the office to get started on designs while the survey is still in progress.
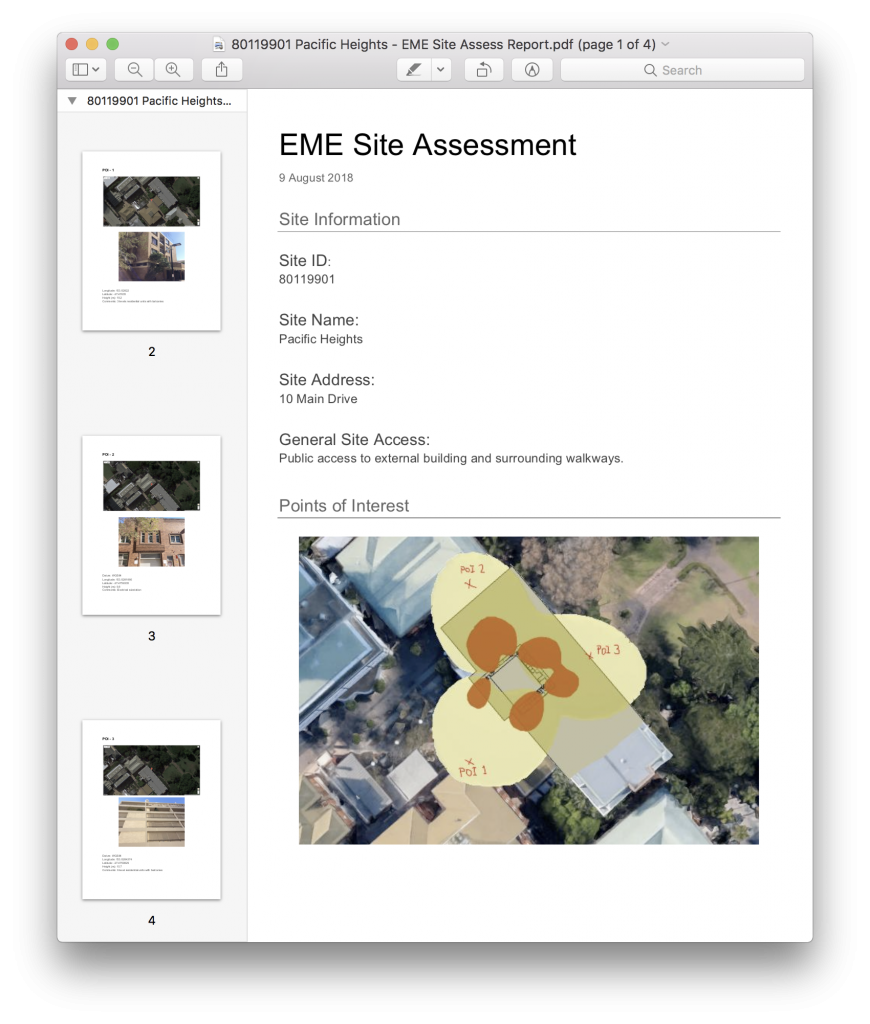
Problem
Our customer was experiencing long delays while waiting to get information back from site. Sometimes, important photos and information was missing and a revisit was needed.
On site, a project manager would walk around with a paper copy of a satellite map overlayed with the site’s EME exclusions zones. They would then identify points of interest (POI) within the zones, take photos and measure the POI’s longitude, latitude and height. All of this information was recorded using paper and a digital camera.
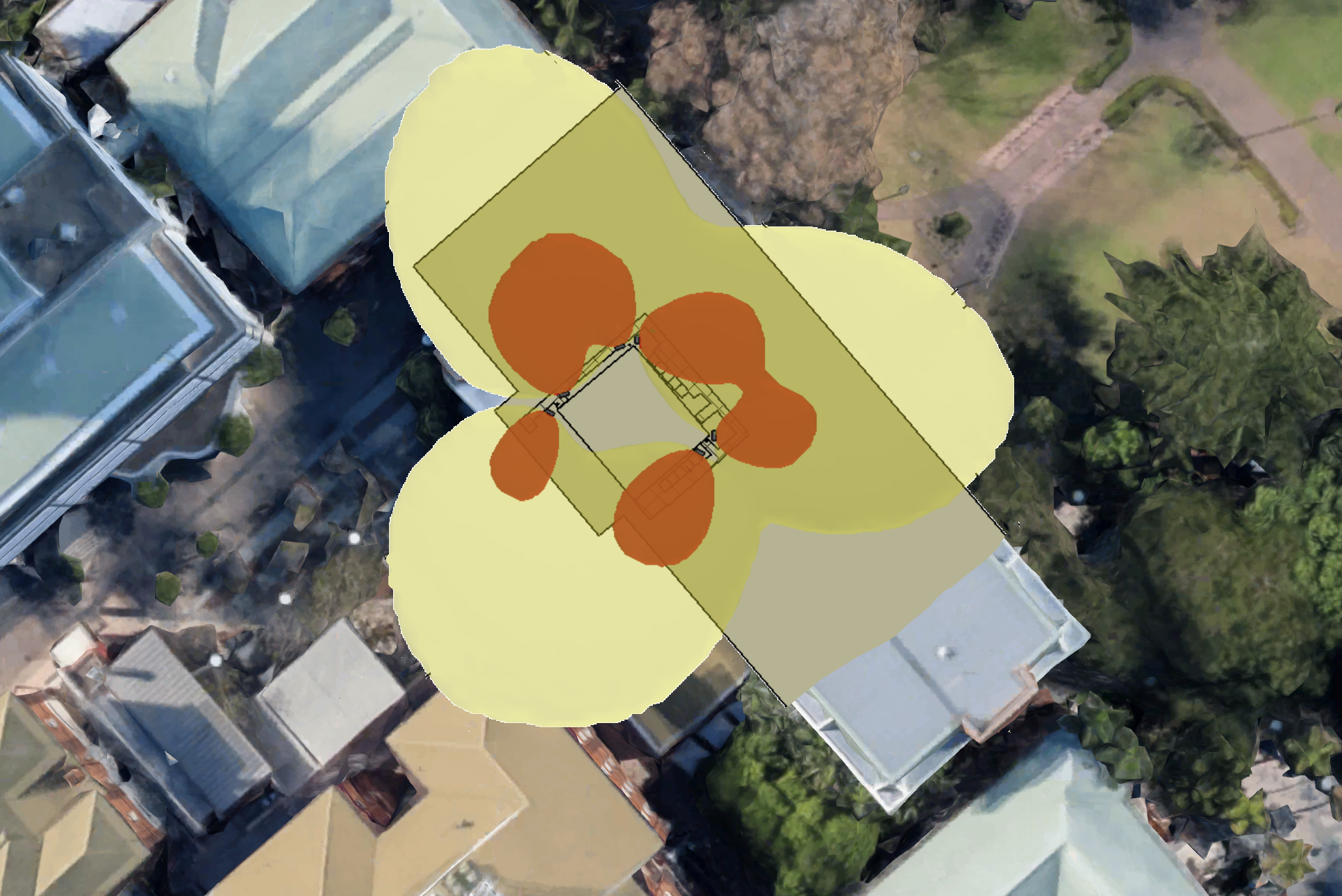
When the survey was over, the project manager would spend around the same time they’d spent on site creating a report. This involved working with the report template their client had supplied and transposing paper answers into the relevant fields. Photos would be downloaded from the camera, resized, named, put in a zip file, and where needed, inserted into the report and emailed back to the office and client.
On top of all this, they would use the POI height and horizontal measurements taken on site to work out the relative height above ground level to the antenna centre. Simple trigonometry, but time consuming nonetheless for project managers who were overworked and desperate for help.
Solution
Speaking to the project manangers, their biggest issue was fatigue. They had too many site visits each week and they couldn’t keep up with the backlog of reports.
Two things got them the most excited: one was our ability to take their legacy report and convert it to a report template so they didn’t have to double handle information; and two, our use of formulas to auto-name photos and calculate POI locations.
Management was more interested in being able to see what was being collected in real-time, and in turn, get their design teams working in parallel. This would then help them win more work, quickly issue invoices, and most importantly, improve their cash flow.
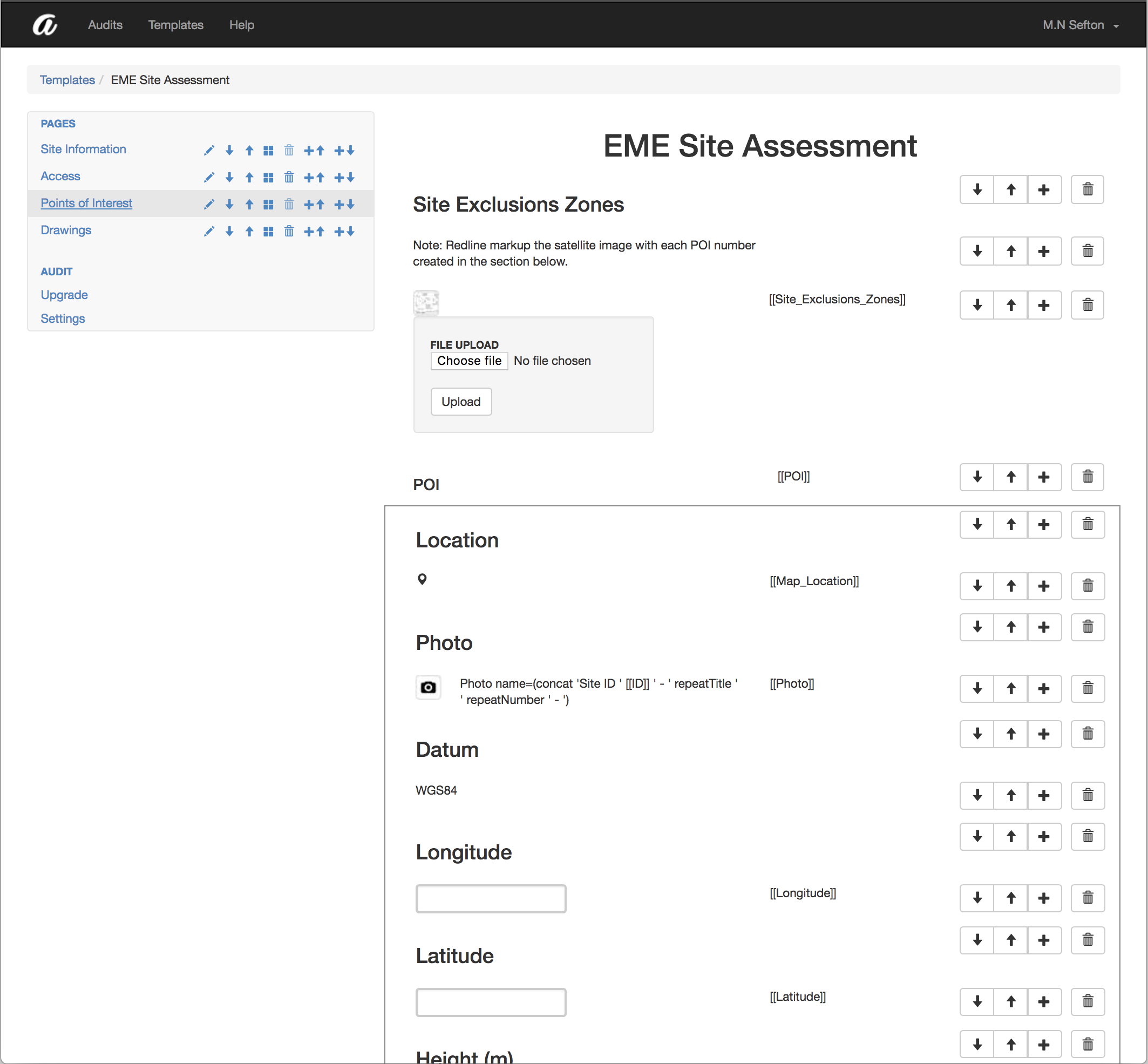
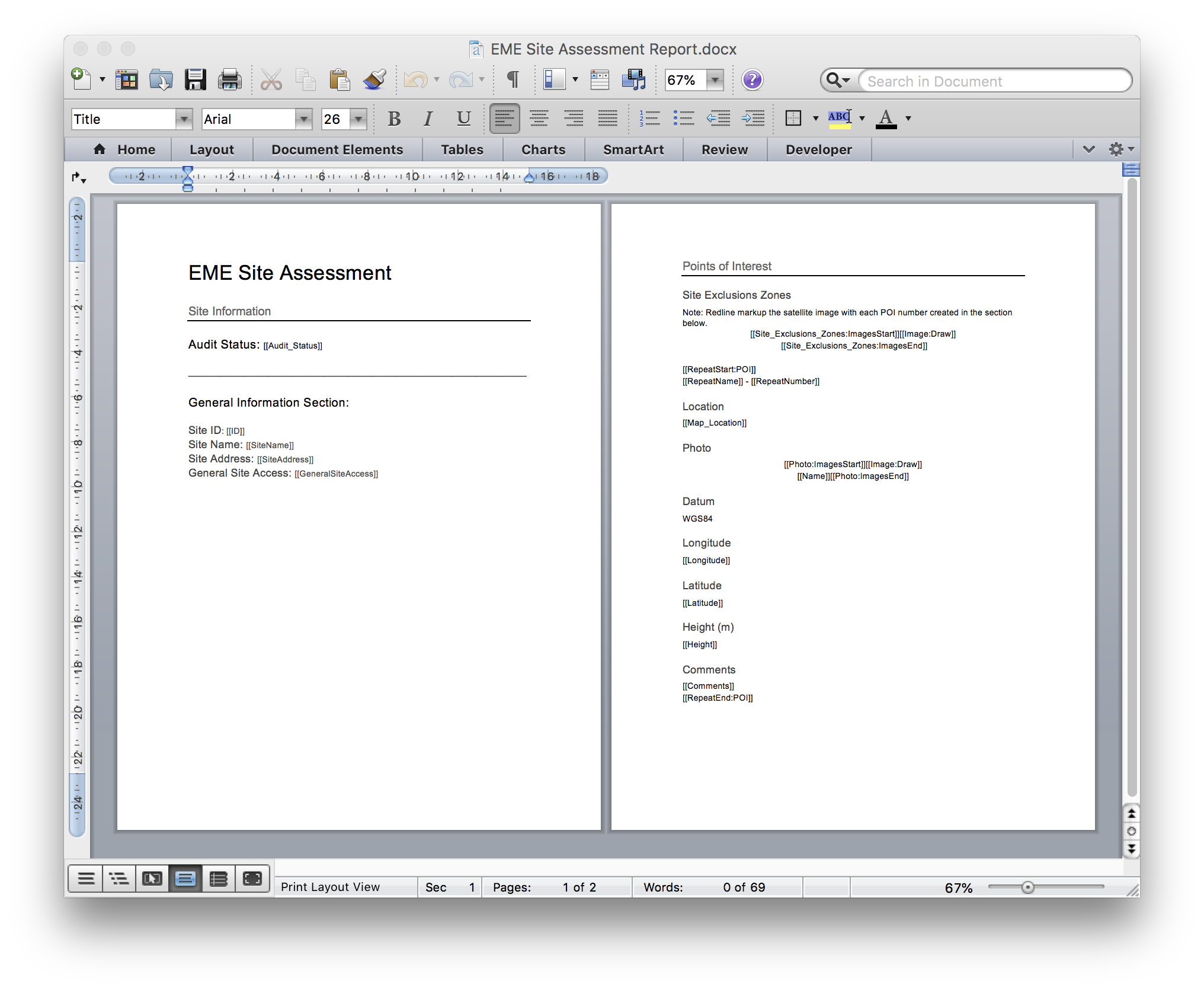
The solution was to take their customer’s report and create an Audicas form template out of it. Then each field name used in the template was inserted into the report to create a report template. Once that was linked to the form template, each time an audit was completed, at the click of the report link, all of the collected information was automatically merged into the report.
What follows is their new, high-level process.
Process
1. Before going to site, a satellite map, overlaid with EME exclusion zones, is uploaded.
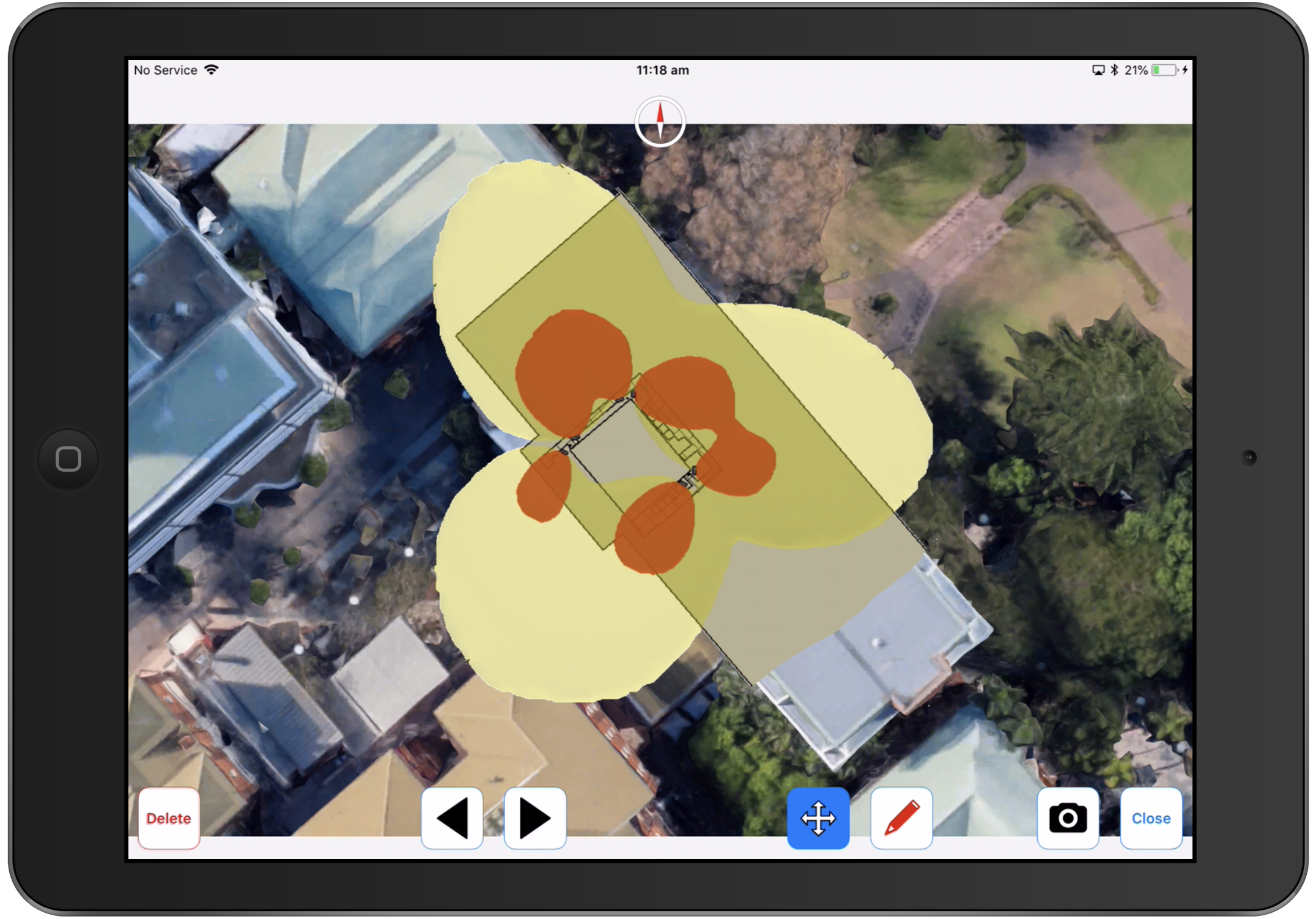
2. As the project manager walks around site, they identify POIs and tap the ‘+ Add POI’ button to start logging it in the form. They also mark it on the satellite map with the POI number just created.
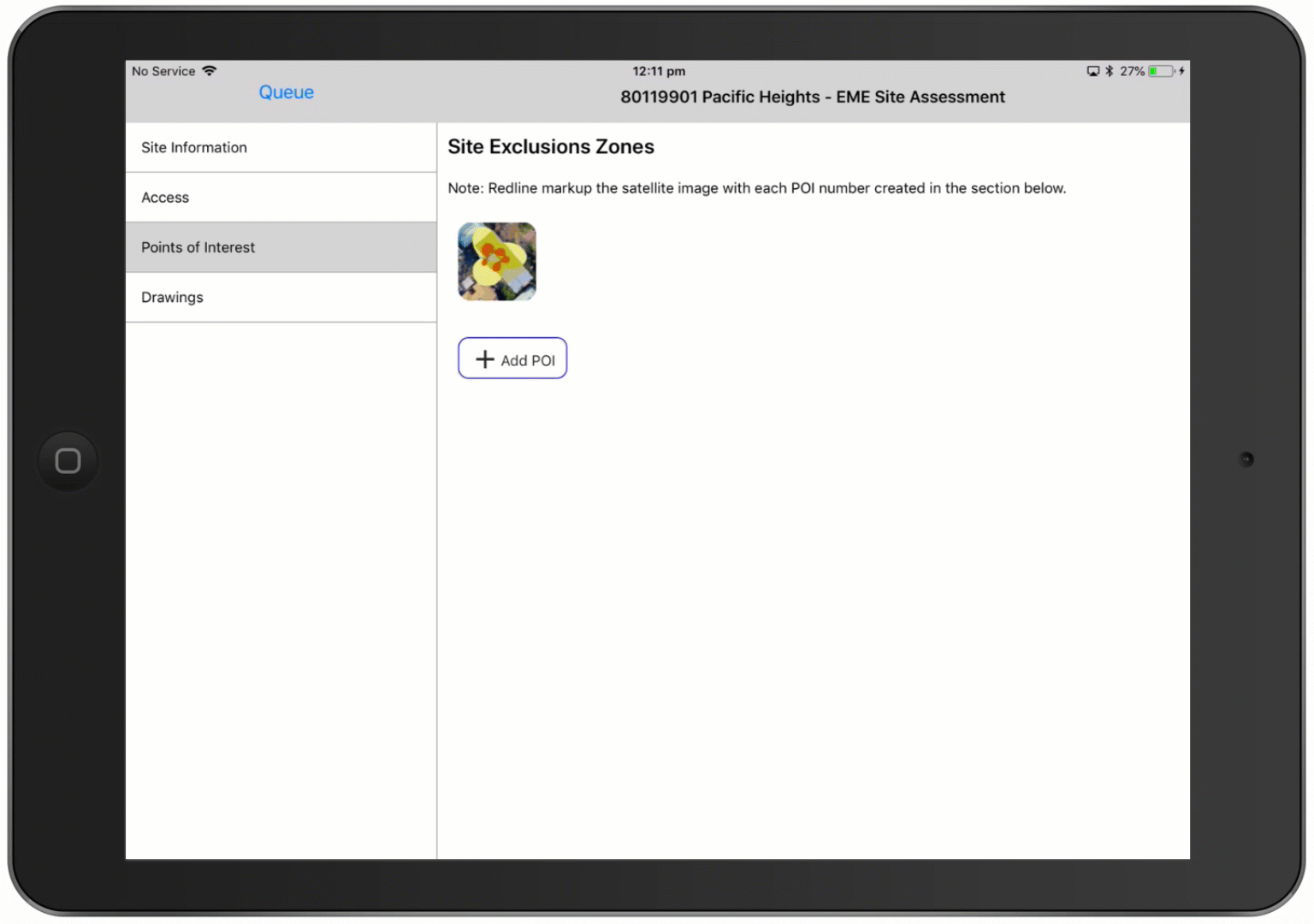
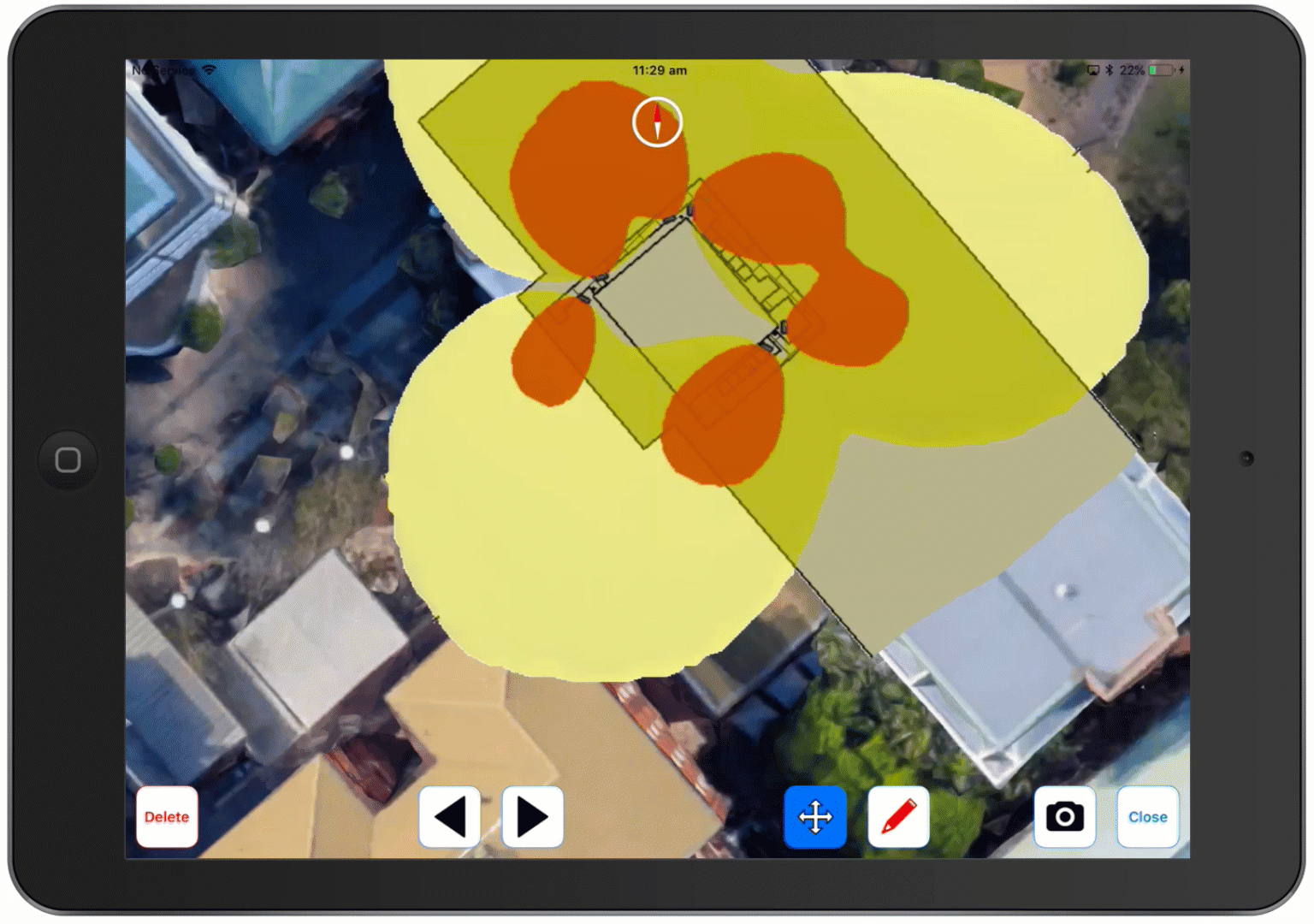
3. In order to get the POI location, they tap the ‘Set Location’ button to open up a satellite map.
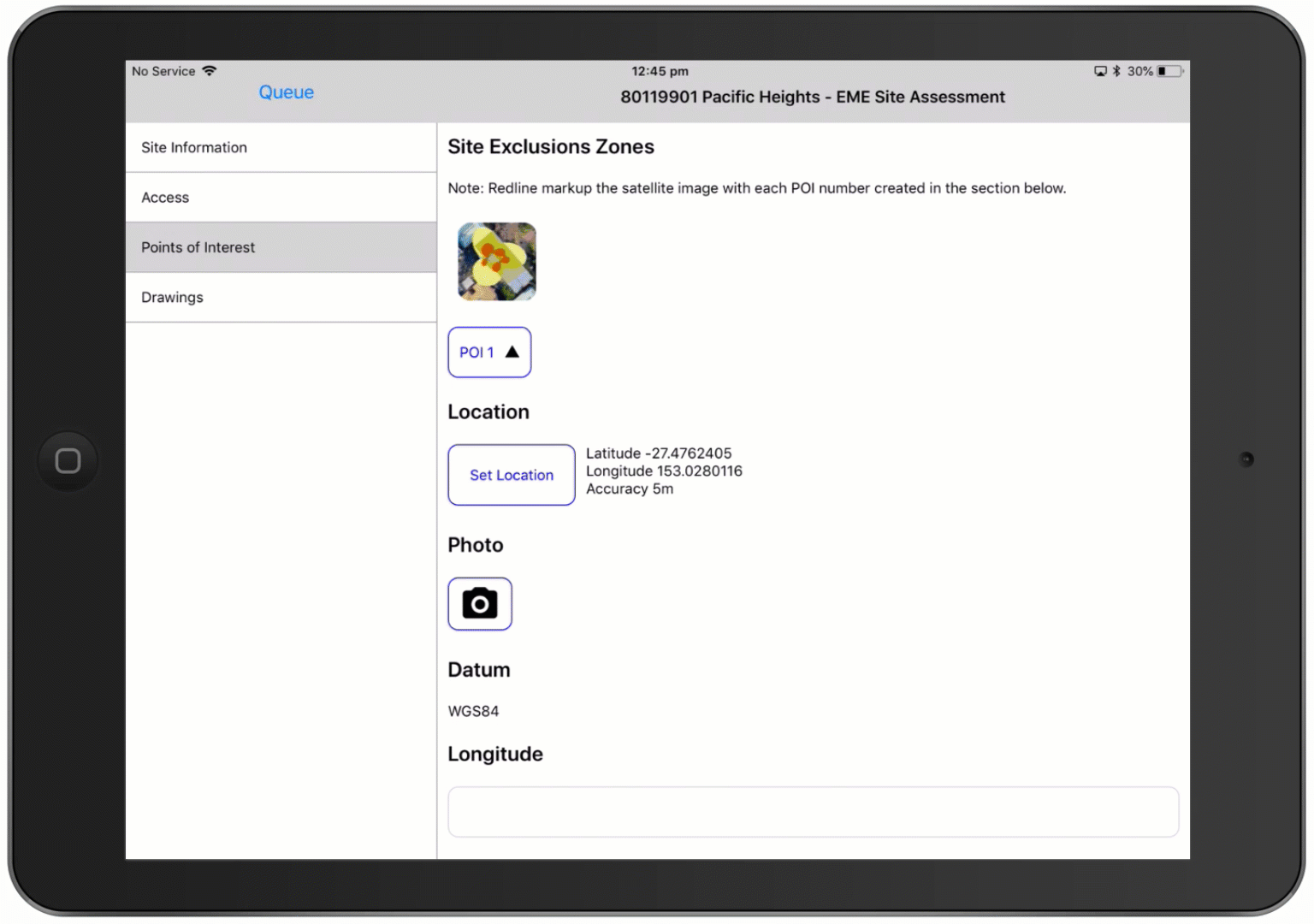
4. When the map opens, in the background it gets the iPad’s geolocation and places a pin at that spot. The project manager then drags it over to the POI to get its location.
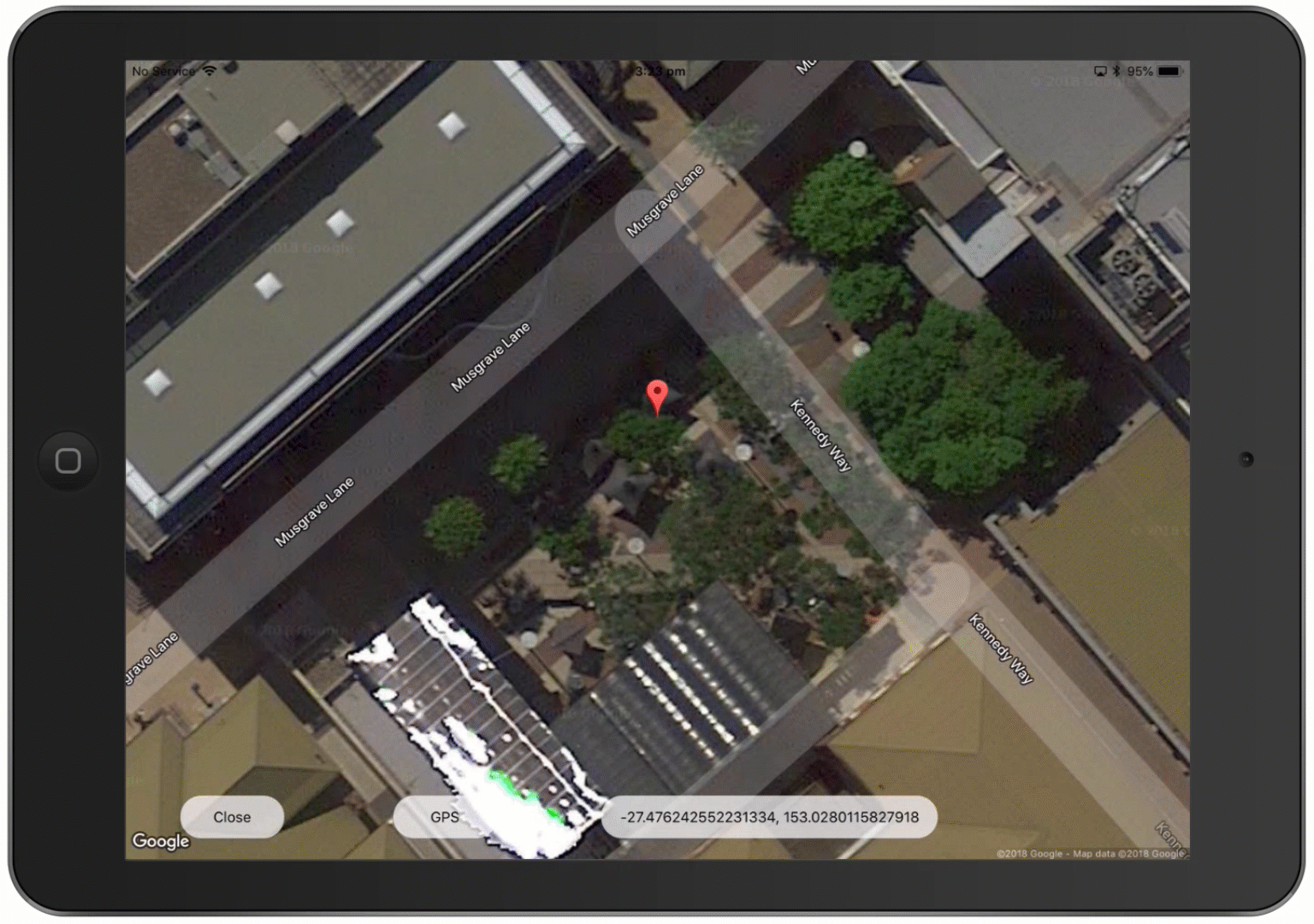
5. For each POI, the project manager uses a laser rangefinder to measure the horizontal and vertical distances. Audicas then uses those inputs to calculate the POI height relative to the antenna centre.
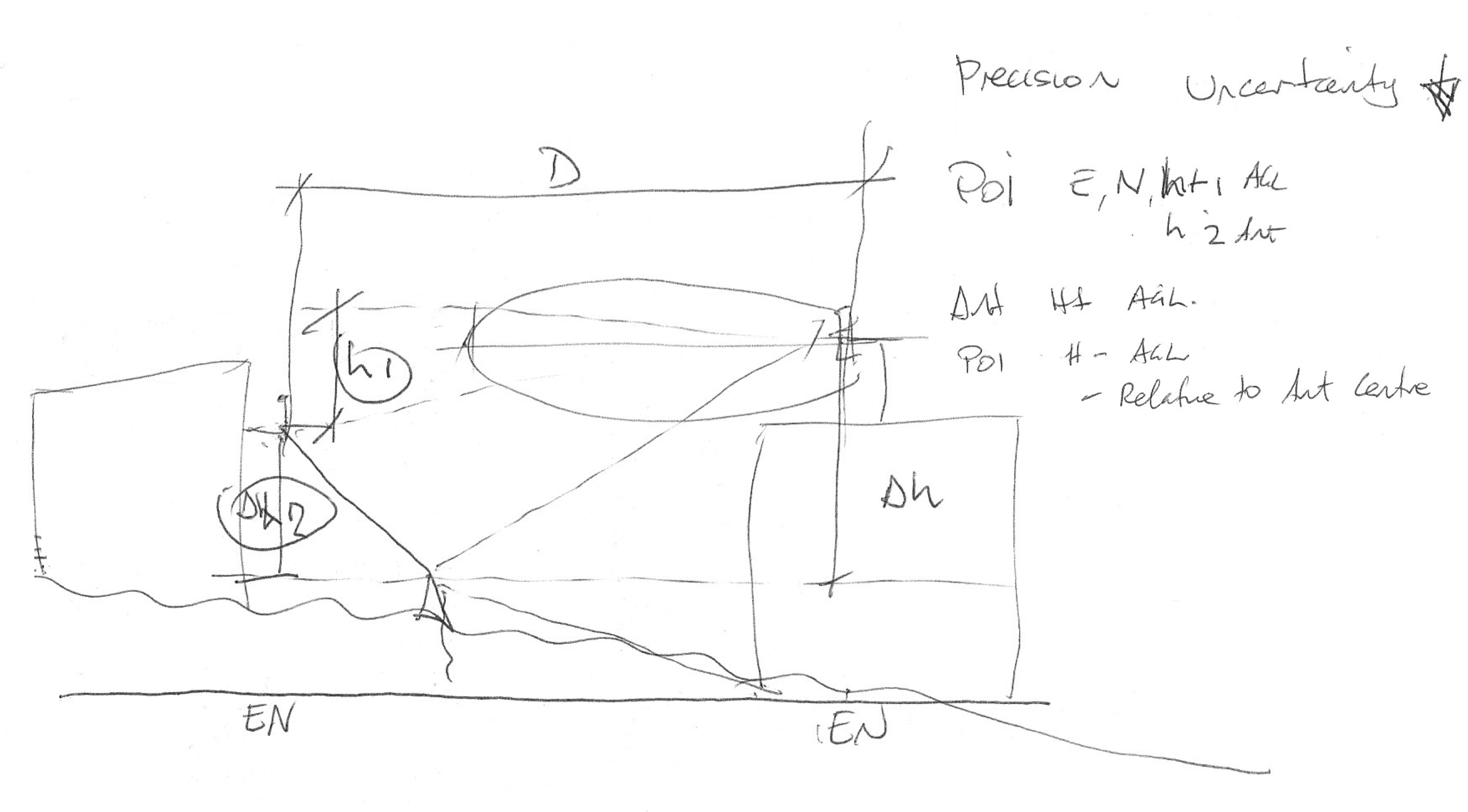
6. As the information is collected, it is sent back to the Audicas admin website for real-time use. If needed, third parties can also be given any level of access from read-only to read-write-delete.
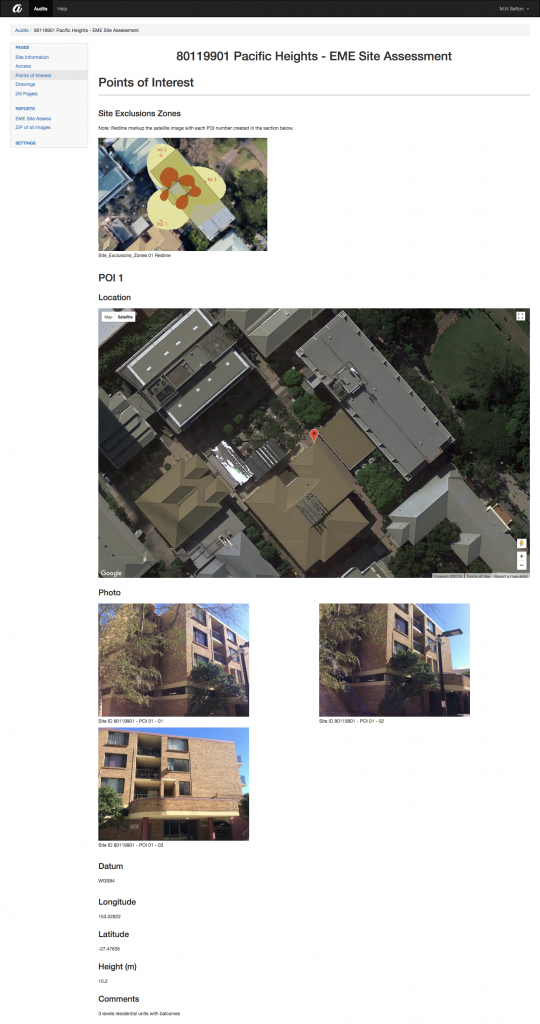
7. From the Audicas admin website, clicking on the links under the report section automatically creates the audit report and zips up all images.
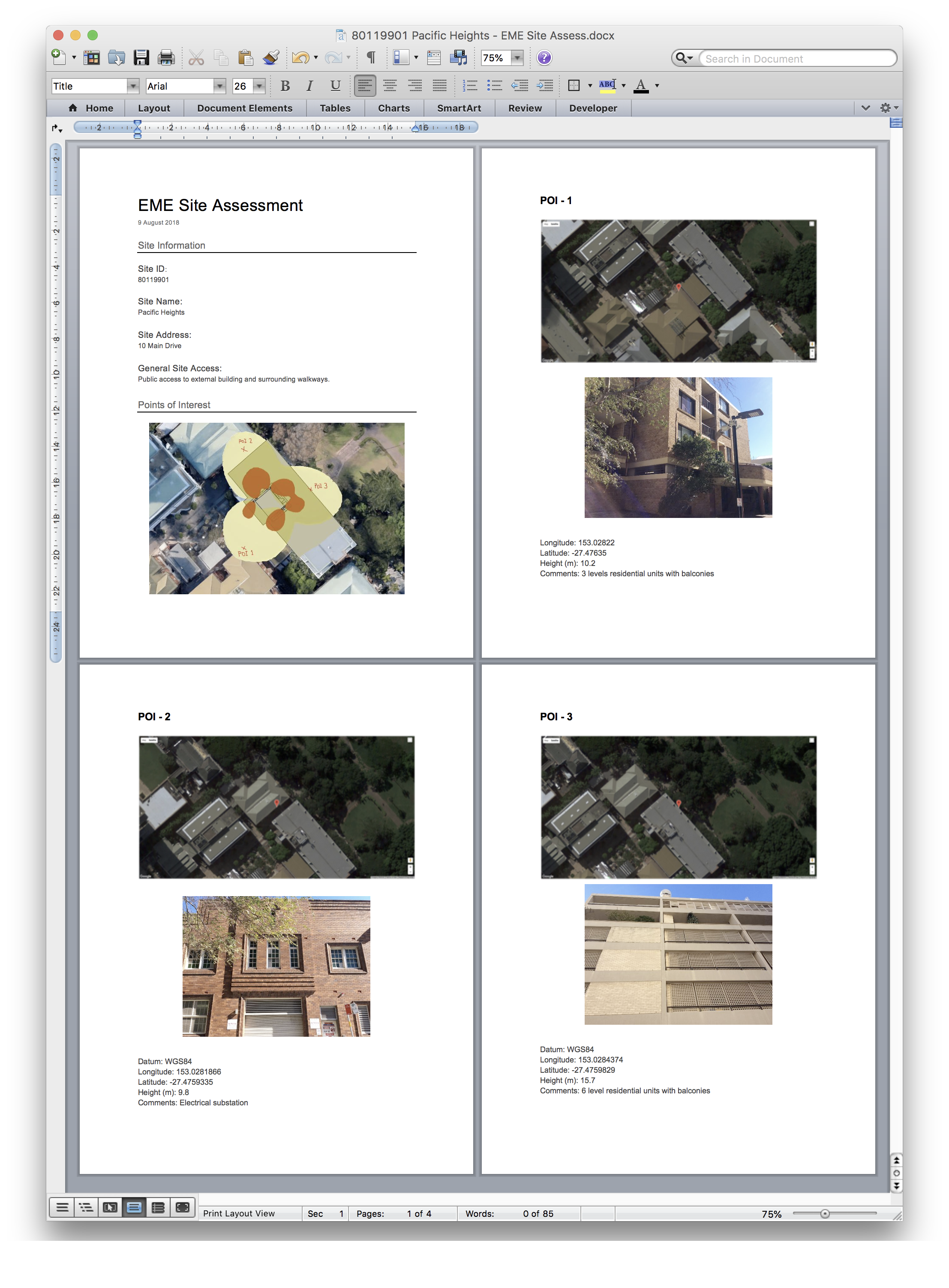
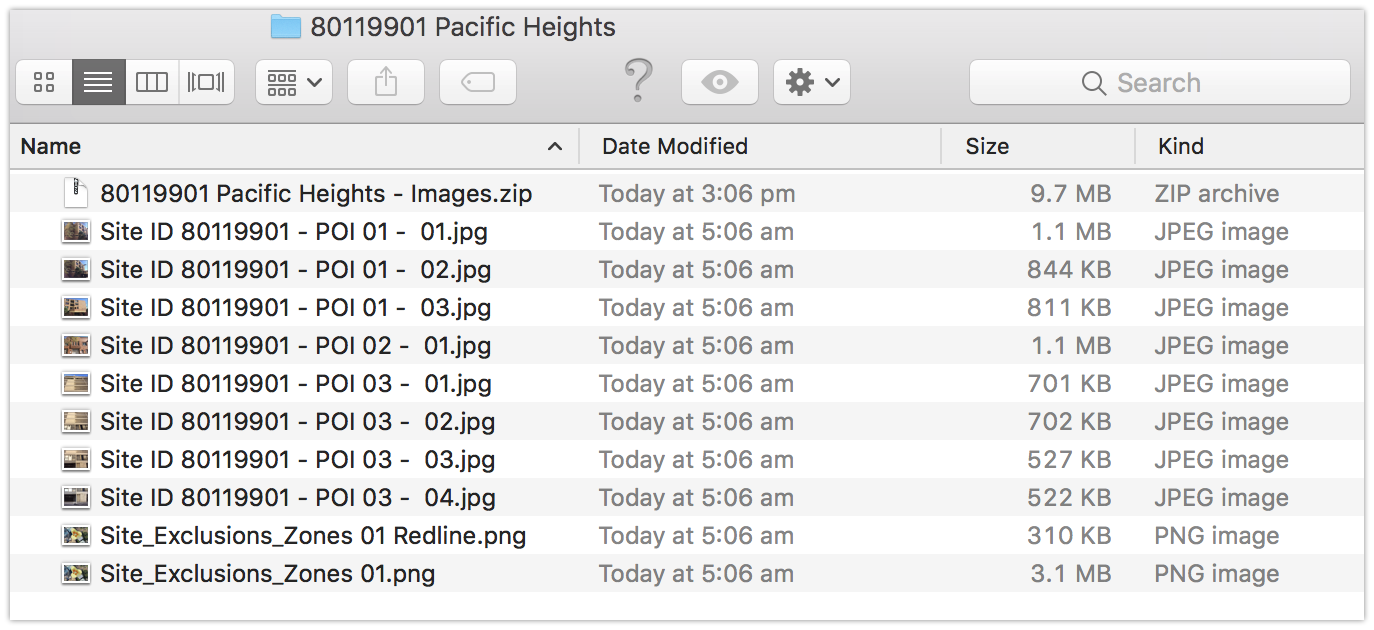
Cost
So, for the example used in this article, the audit form and report template took around half a day to create. However, for a typical report of average length, it takes around four days to set everything up.
Deploying Audicas on an iPad takes 30 seconds. User training takes 30 minutes at most and can be done in a group via a webinar.
So, for an average project, we could get you up and running in one week. Yes, you read right. One week!
Total cost for five users and all of the above setup would be in the order of AUD7,000 (+GST). That’s in the first year. From then on, each year your subscription would be in the order of AUD3,000 (+GST).
So, now that you know the ballpark cost and time to setup, how long do you think it would take you to breakeven? What benefits could having a efficient solution like Audicas have on your team, project and cashflow?