Audicas asset audits helps a billion dollar company achieve the impossible!
To realise the full value of their recently implemented asset management system, a broadcast infrastructure company needed to collect asset hierarchy information for their 100,000 plus ground based assets in an extremely short period of time.
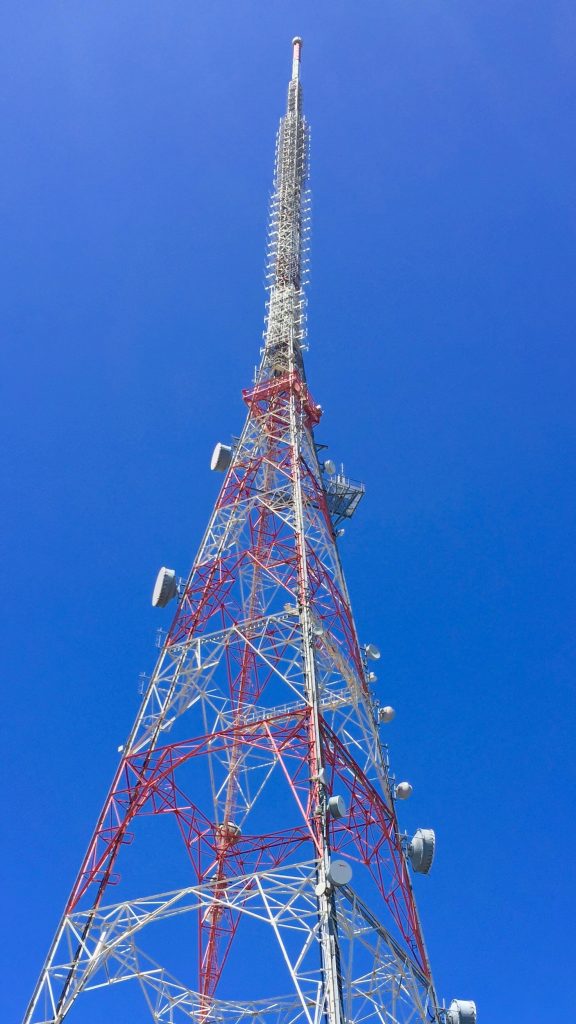
Background
Having a portfolio of over 600 sites, with many in remote and hard to get at places, the company needed a software tool to quickly collect information, be able to work offline, and have software improvements and fixes deployed in real-time. And whenever an internet connection was available, automatically send all asset information, including photos, back to their project office.
Audicas was approached after they had first experimented with using another solution, which for various reasons, did not work as expected. Unfortunately, the delivery date was fixed, so only 3 months remained.
Undaunted, the Audicas project team held a series of meetings over a week to fully understand the project requirements.
What we learnt was that a field tech would go to a site and walk from building to building, room to room, searching for assets. Most of them had been barcoded in the past, so they would check it against a long list of assets.
When found, the asset would be identified using a asset hierarchy list (E.g. system / sub-system / description) and a series of questions would be answered and photos taken.
Newly found assets would have a barcode attached and they would then follow the same process as that used on “known” assets.
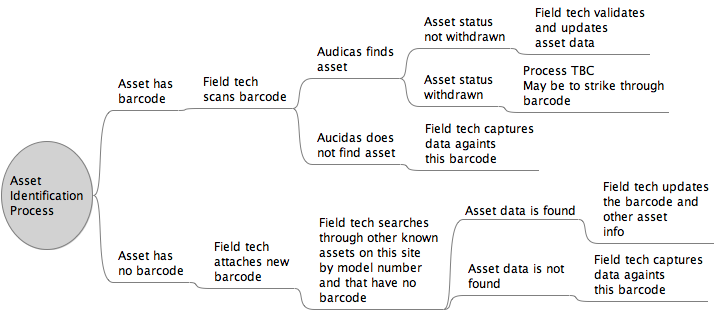
Solution
With only 3 months to work with, we realised that we’d have to move fast and use as much of Audicas’ existing functionality as possible. The scope would have to be laser focused.
Using the Audicas Asset Module, we created an asset database and loaded it up with their asset data.
We then created an asset inspection form for the Audicas iPad app which stored a site’s asset information on a hidden, “unassigned” asset page.
Then Audicas’ hierarchy buttons were used to give the field techs a quick way to capture the asset hierarchy information.
Finally, Audicas’ barcode scanner was configured to search through the list of “unassigned” assets and when found, assign the asset to the page/system the field tech was currently looking at.
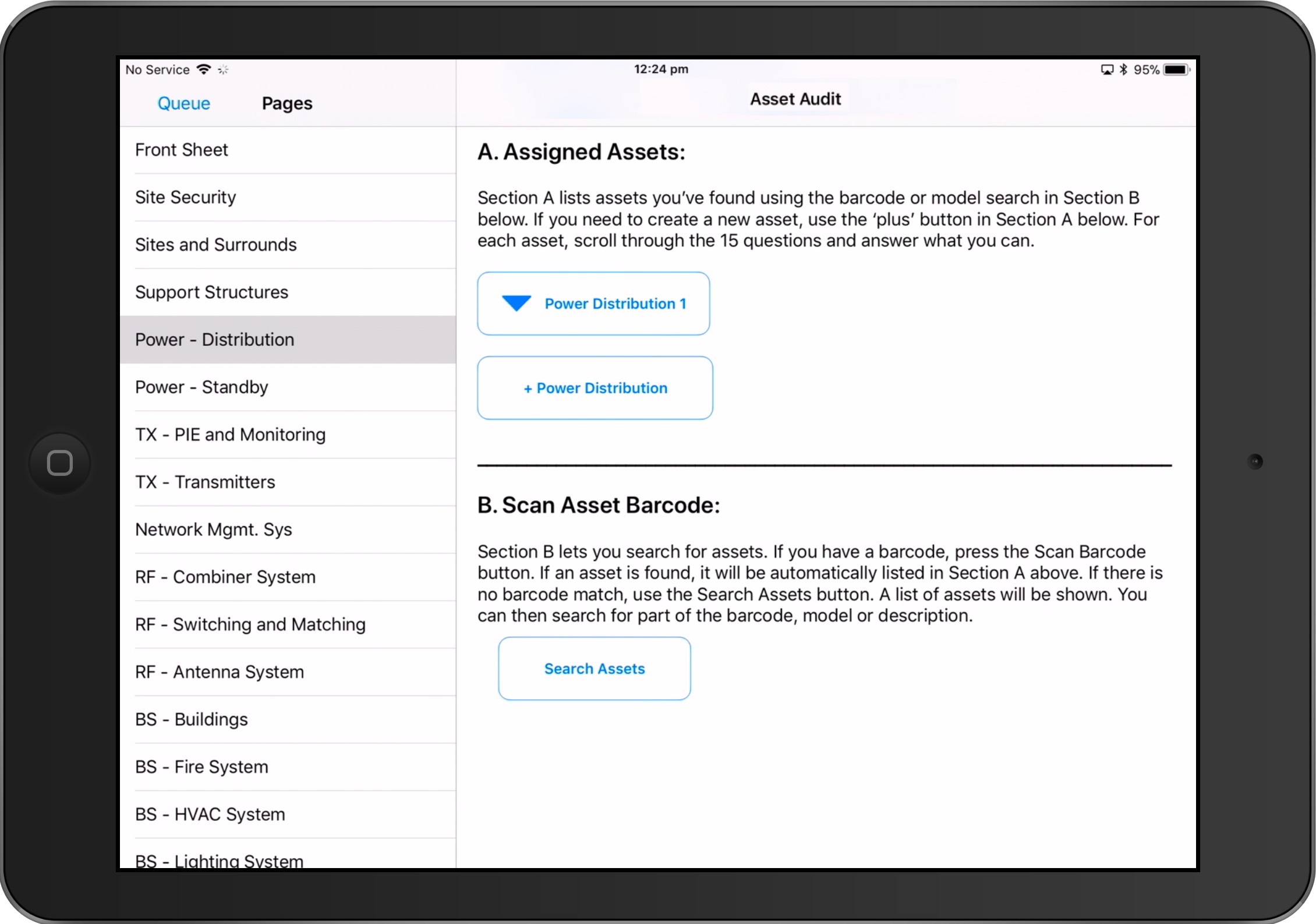
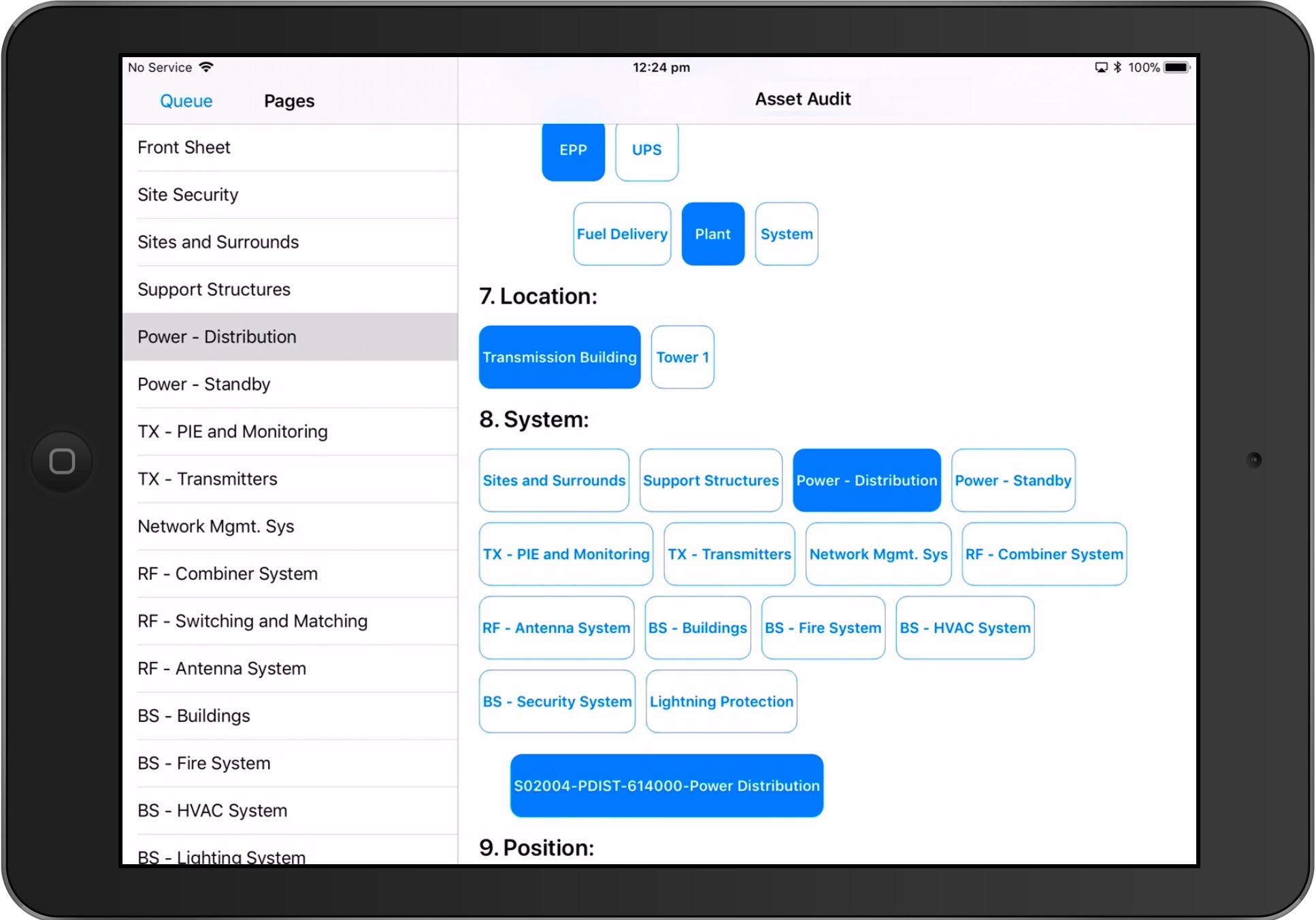
Benefits
From the field tech’s perspective, having Audicas on a lightweight iPad versus a laptop was a big plus.
The layout of the form and size of the buttons and other interactive components was easy for them to use.
Having everything running in the background, being synchronised and upgraded without their input, gave them time to focus on collecting quality information.
For the business, having a working solution two weeks after they had engaged Audicas was a huge benefit. Then receiving ongoing support and customisation during the project gave them confidence that the project was going to be completed successfully.
In the financial year after the asset hierarchy information was gathered, the company is getting full benefit from the asset data collected and imported into their asset management system.
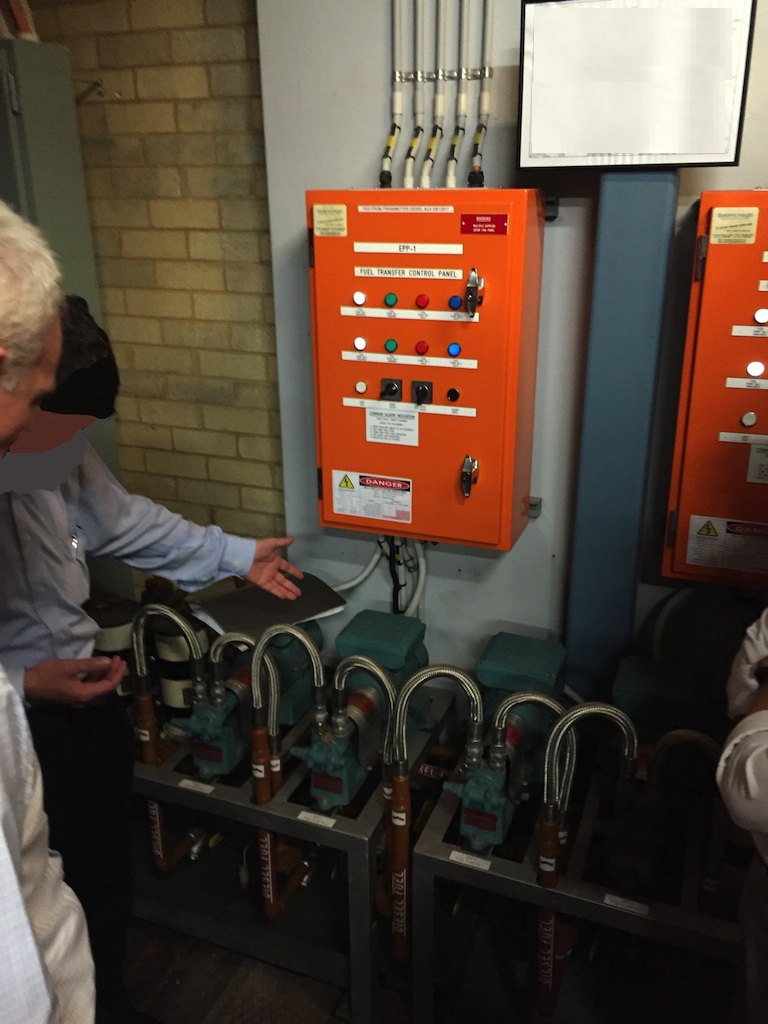
Within two weeks we had deployed Audicas and trained a core group of field techs who then trained the remainder. They then started fanning out across the country to visit sites and give us feedback.
The asset audit form was improved, bugs fixed and all of the upgrades were pushed out in real-time with no need for the field techs to send their iPads back to head office.
Significantly, the project was a big success and when it was completed, all of the new and updated asset information was exported from Audicas back into their asset management system.
As a bonus, they also received a large library of site photos which had been automatically named and categorised by Audicas for quick and efficient searches.